In the realm of automotive development, the Electronic Control Unit (ECU) is a pivotal component that governs various functions within modern vehicles, ranging from engine management to advanced driver-assistance systems (ADAS). As vehicles become more complex, ensuring the safety, reliability, and performance of these ECUs is paramount. This is where rigorous validation strategies come into play, employing Model-Based Design (MBD) methodologies to facilitate comprehensive testing at various stages of development. The key validation stages—Model in the Loop (MIL), Software in the Loop (SIL), and Hardware in the Loop (HIL)—are integral to this process, offering a structured approach to mitigate risks and optimize the performance of automotive ECUs.
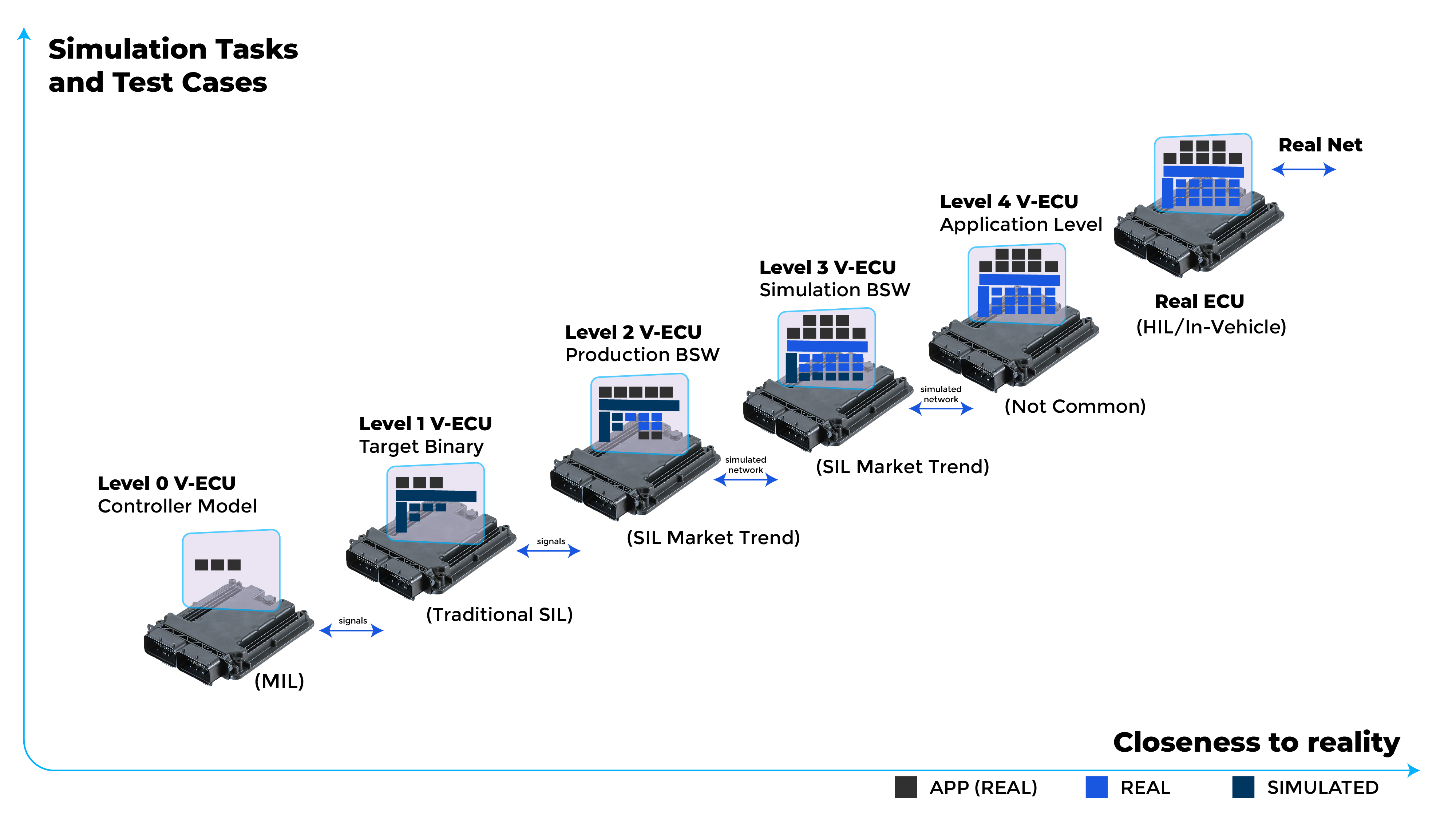
Model in the Loop (MIL)
Objective: To validate the controller logic within a high-level simulation environment before any hardware or code implementation.
Methodology: In MIL, the System Under Test (SUT) consists of two components:
- The plant model, representing the physical system.
- The controller model, representing control algorithms.
These models are run in a simulation environment, typically MATLAB/Simulink, allowing engineers to test the controller logic across a variety of scenarios. The model isn’t hardware-specific, facilitating rapid iterations and design refinements before moving to the next development stages.
- Simulation Fidelity: The degree of realism of the plant model is crucial, as it directly influences the reliability of MIL testing. Parameters such as response time, dynamics, and environmental conditions need to be meticulously modeled to reflect real-world behavior.
- Control Strategy: MIL focuses on verifying the control strategies, such as Proportional-Integral-Derivative (PID) tuning, state estimation, and fault detection algorithms. The goal is to ensure that the controller logic performs as expected across a range of operating conditions.
- Debugging Capabilities: MIL environments offer extensive debugging tools, allowing engineers to visualize signal flows, track data, and analyze the behavior of control algorithms in a controlled setting.
Benefits: MIL testing provides early insights into potential design flaws or logical errors in the control algorithms. By validating the controller logic in a simulated environment, engineers can refine their designs before moving on to more resource-intensive testing phases.
Software in the Loop (SIL)
Objective: To validate that the control algorithms can be accurately converted into executable code, ensuring that the functionality remains consistent within a software environment.
Methodology: In SIL testing, the model is already in software form. The primary change is that the control block within this model is automatically translated into C or C++ code using tools like Simulink Coder. This newly generated code replaces the control block in the simulation, while the rest of the model remains in its original software form.
- Code Generation: The auto-generated code undergoes rigorous testing to ensure it adheres to coding standards and maintains functional consistency with the original software model. Key metrics such as code coverage, execution time, and memory usage are closely monitored.
- Compiler and Platform Considerations: SIL testing also examines the impact of different compilers and target platforms. Variations in compiler optimizations can influence the execution of the control code, making validation across multiple toolchains essential.
- Integration Testing: SIL facilitates early integration testing, allowing the evaluation of the code’s interaction with other software components. This process helps identify potential issues related to data communication, concurrency, and timing that could impact overall system performance.
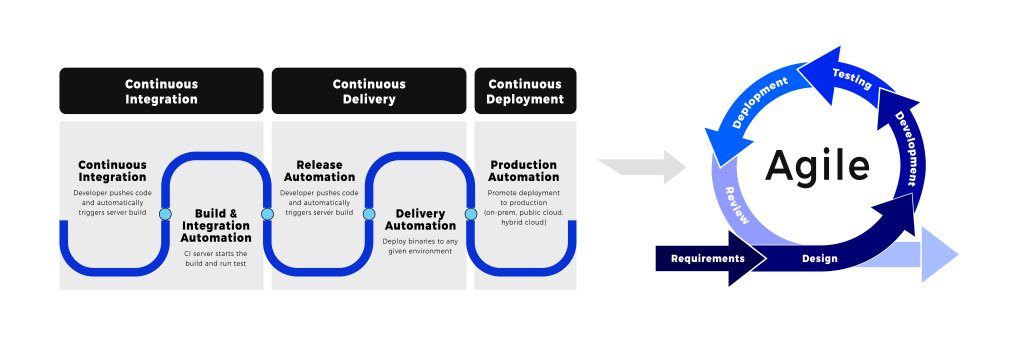
Benefits: SIL testing ensures that the control algorithms behave as intended when executed as software, bridging the gap between model-based design and real-world implementation. This approach minimizes the risk of software bugs and performance issues in later development stages.
Hardware in the Loop (HIL)
Objective: To validate the integrated system, including both the ECU hardware and software, under realistic operating conditions.
Methodology: HIL testing involves connecting the embedded processor (with the validated control software) to real or simulated hardware interfaces. The plant model is executed on a real-time simulator, such as dSPACE or National Instruments systems, which interacts with the ECU as if it were controlling a real vehicle.
- I/O Interface Testing: HIL testing rigorously evaluates the ECU’s I/O interfaces, including analog and digital inputs/outputs, communication protocols (e.g., CAN, LIN, FlexRay), and sensor/actuator integration. This ensures that the ECU can accurately interpret sensor data and control actuators in real-time.
- Fault Injection: HIL setups often include fault injection capabilities, allowing engineers to simulate faults such as sensor failures, communication errors, or actuator malfunctions. This helps validate the ECU’s fault detection and mitigation strategies.
- System-Level Validation: HIL testing is the closest approximation to real-world conditions before deployment. It tests the entire system’s performance, including control loops, response times, and interaction with other vehicle systems, ensuring the ECU performs reliably in the intended operational environment.
Benefits: HIL testing provides the final layer of validation, ensuring that the ECU operates correctly in a near-real environment. By simulating real-world conditions, HIL testing uncovers issues related to hardware integration, system-level interactions, and overall system robustness, reducing the risk of failures in the field.
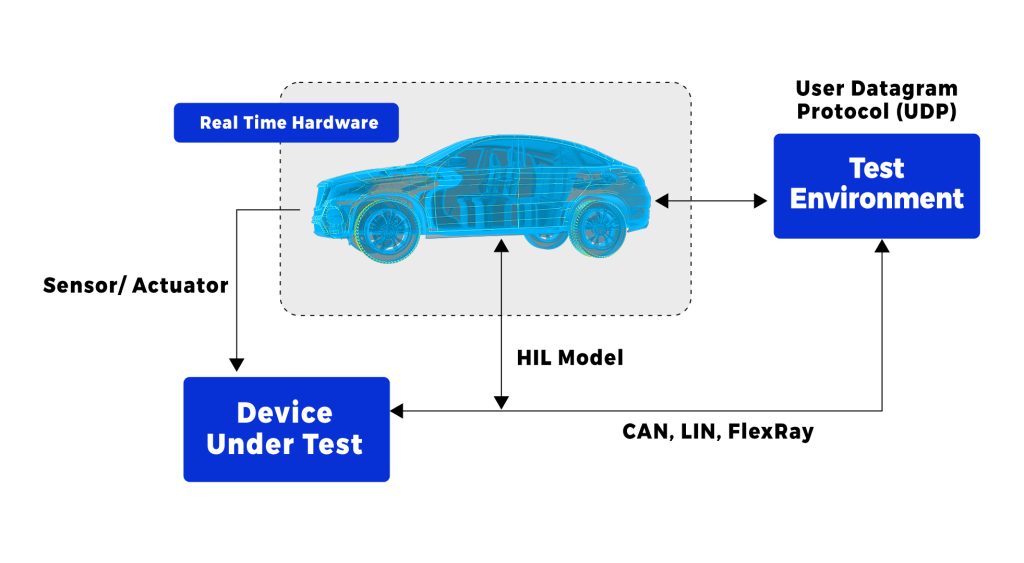
VVDN’s Expertise in ECU Validation: Empowering Automotive OEMs and Tier 1 Suppliers
With over a decade of experience in software, product engineering, testing, and manufacturing, VVDN develops a wide range of automotive solutions for OEMs and Tier-1 suppliers. Our deep expertise in automotive-grade product development, combined with cutting-edge testing facilities, enables us to tackle the most complex validation challenges in the industry.
Additionally, as an authorized channel partner for world-leading test and measurement instrument manufacturers, VVDN is equipped with the latest technology to perform rigorous, safety-critical testing. Our skilled testing team excels in managing the intricacies of system integration, ensuring that ECUs not only meet but exceed regulatory compliance standards. By leveraging our comprehensive testing services, automotive companies can confidently bring high-quality, reliable, and safe ECUs to market, ensuring the seamless functionality and security required in today’s vehicles.
To learn more about our offerings and discuss how we can collaborate to meet your testing requirements, please contact us at info@vvdntech.com